Our Services
Ground Transportation
Network Design and Optimization
Ground Coordination With Air/Ocean Movements
Optimized FTL and LTL Movement
Dedicated Carriage and Private Networks
Leveraged and/or shared private networks
Purpose-built infrastructure
White Glove/Specialized Transportation
Oversize, Overweight, Special Equipment and Projects
Listen To Our Deep Dive Podcast And Read A Case Study
Ground Transportation Podcast
Ground Transportation Case Study
Supply Chain Optimization
Financial Optimization
Inventory On Demand: Third-party Inventory Ownership
Inventory Financing Solutions
Finance Services for Supply Chain Enterprises
IT Support
API, Carrier and ERP Connection Services
Custom Services for Supply Chain Enterprises
Consulting Services
Ground Transportation Evaluation and Optimization
RFP Consulting, Analytics and Optimization
Damage Minimization Solutions
Read Our Optimization Case Studies And Watch The Video Podcast
Read The Case Studies
Watch A Video Podcast
Supply Chain Control Towers
Management Services
Supply Chain Health Monitoring and Analytics
Carrier Management and Collaboration
Third Party Shipment and Exception Management
Technology Services
FlexShip TMS (Multi-carrier Freight Management Platform)
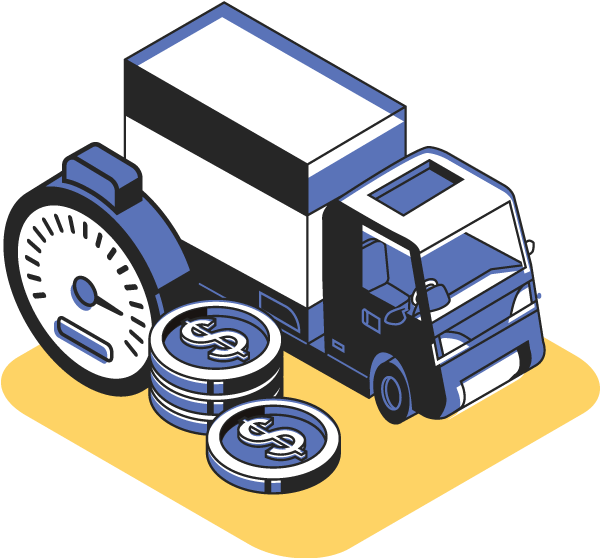
Ground Transportation
Move Better: Transforming shipments into orchestrated movement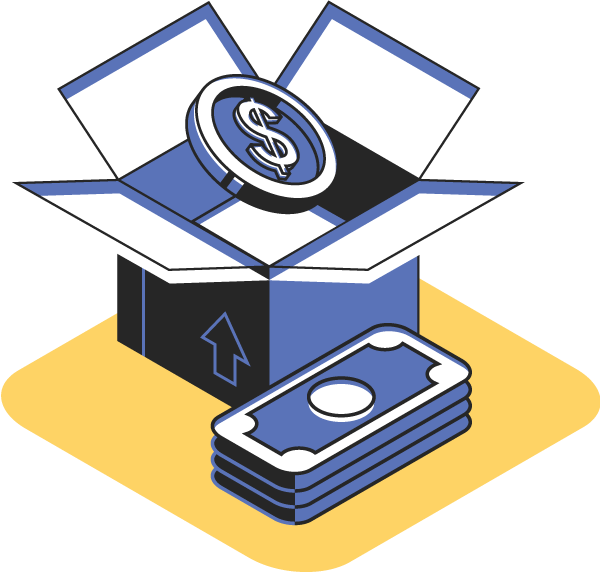
Supply Chain Optimization
Redefine Better: Streamlining supply chains with new and collaborative approaches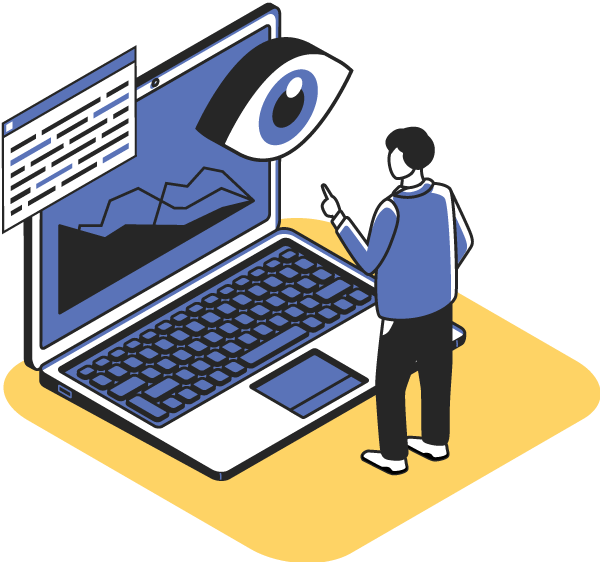
Supply Chain Control Towers
Control Better: Bringing tangible value to complex supply chains with simple, flexible visibility and management solutionsSupply Chain Visibility
Shipment processing
Automated dispatching
Warehouse Dock Scheduling
Other Technology Services
Cross-carrier Connections
Network Edge Applications and Carrier Connection APIs
Real-time Condition Monitoring (Temperature, Humidity, Tampering, Shock, etc.)
ERP Integration for Multi-carrier Supply Chains
Supply Chain Cost Normalization
Analytics Integration for Data Visualization Platforms
Integrated Solutions: People + Technology
LSP and Supplier Collaboration
Outsourced and Optimized Manual Work Solutions
Continuous Improvement Analytics
Exception Management and Resolution
Virtual White Glove Transportation Solutions
Expedited Freight (Ground/Air)
Time-definite Delivery And Urgent Logistics and Multi-party Supplier Coordination
Specialized Freight and Capital Equipment
Logistics Management
Industry-specific solutions: Cold chain, provenance, compliance, high-value goods
Quarterly Carrier Review Processes (QBR)
Benefits to You
Client Results
Resources